Used for daily cutting management and progress control
Spring Overseas, located in Delhi, India, has been doing business with well-known Japanese brands since 1980, and is well known for its high quality and quick delivery as an Indian manufacturer.
The president, Mr. Satish Chand, himself studied in Japan as a student, specializing in fashion and katagami, so it is no wonder that he has a deep understanding of Japan.
As a side note, when InfoEye was founded, it was started in a corner of Spring Overseas’ factory.
■ Devices used: PC, Mac, iPad
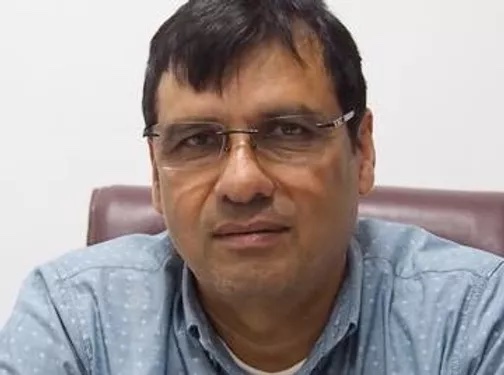
Mr. Satish M. Chand, Representative Director
○ Improved inspection accuracy
At Spring Overseas, all orders are registered in the InfoEye system for thorough progress management. In addition to cutting management for each line, this system is also used to manage orders for fabric and other materials related to production.
Since all orders are linked to profitability management and delivery date management, it is easy to check inefficient production lines and identify products with high loss rates.
○ Strict quality standards and production control
Production management work tends to be a very personal job.
At Spring Overseas, we prevent any problems from occurring by systematizing the process.